ESSENTIALS
An essential line of daily products to support the basic needs of the user. Based off the first tier highlighted by Pavlov, psychological needs, air, water, food, heat, clothes, reproduction, shelter, sleep.
This projects aims to test my ability to think critically to create a replication of an existing product, create a new iteration, or design a revolutionary product aimed at support the first tier needs. Each item on the list will be addressed separately unless I can consolidate a solution.
Research & Discovery
Understand the problem and the target audience. How does the user want to use the product. Analyse competitor benchmarks and trend insights.
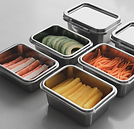


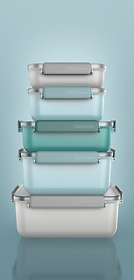
Various shapes, materials,
and closures.
Define Requirements
Set goals, objectives, and deliverables. Gather constraints (eg. budget, time, technology)
Ideation
Brainstorm ideas and concepts. Sketch or wireframe potential solutions.
Concept Development
Choose the best ideas to develop further. Refine the concept with feedback from stakeholders.
Design
Create high-fidelity designs. Develop high-quality prototypes or mockups with high standards. Implement specific materials and finishes. The original vision must remain the same from concept to production
Review & Feedback
Validate the final form by testing every feature and use case. Present the design for feedback from stakeholders. Iterate and adjust based on input.
Finalisation
Finalilse design assets and documentation. Prepare for implementation or production,
Testing & Validation
Test design with users or in real-world scenarios. Collect feedback for improvements.
ChatGPT Design Structure: 1. Conceptualization and ResearchDefine Product Requirements:Clearly outline the essential features of each product. Consider size, weight, functionality, durability, and materials, as well as any additional features (e.g., leak-proof for the water bottle, airtight for the food container).Target Price Point:Identify a target price range that reflects affordability while ensuring durability and quality.Material Research:Research materials that are durable yet cost-effective. For example:Metal Water Bottle: Stainless steel is durable, but alternatives like aluminum could be lighter and cheaper.Glass Food Container: Consider borosilicate glass (more durable but pricier) or tempered glass.Lunch Bag: Explore fabrics like nylon or polyester, which are affordable, durable, and easy to clean.Competitive Analysis:Look at existing products on the market that meet similar needs. Analyze their materials, design, and pricing. Note what works and what could be improved upon.2. Design PhaseSketch the Design:Start by sketching or using design software (e.g., AutoCAD, SolidWorks) to visualize the products. Consider aesthetics, functionality, ease of use, and ergonomics.Prototyping:Create initial prototypes using low-cost materials or 3D printing. For the lunch bag, you can create a simple hand-sewn prototype; for the water bottle and food container, consider making small-scale models from inexpensive materials.Test Durability and Usability:Test the prototypes for strength, ease of use, leak-proof capabilities, and other functional requirements. Identify any design flaws or areas that need improvement.Refine the Design:Based on testing feedback, adjust dimensions, materials, and features to improve performance and lower cost.3. Material SelectionCost vs. Durability Balance:Choose materials that offer the best balance between durability and cost. For example:Water Bottle: If stainless steel is too expensive, aluminum might be a viable alternative.Glass Food Container: Look for affordable tempered glass or use BPA-free plastic with good durability ratings if glass becomes too costly.Lunch Bag: Look into high-quality yet affordable fabrics like recycled polyester or nylon.Sourcing Suppliers:Identify reliable material suppliers who can provide consistent quality at your target price point. Request samples for quality testing.4. Final Design and EngineeringRefine the Design for Manufacturing:Once you've selected materials, work on refining the design for manufacturing. This includes detailing production processes and ensuring the product is optimized for low-cost production.Design for Manufacturability (DFM):Ensure that the design is easy to manufacture at scale. Avoid overly complex features that may increase cost or require specialized equipment. Consider factors like moldability, tooling costs, and ease of assembly.5. Prototyping the Final ProductCreate High-Fidelity Prototypes:Once the design is finalized, create high-quality prototypes using the chosen materials. Work with a manufacturer or local fabricators to produce these prototypes.Testing:Conduct thorough testing (e.g., drop tests for durability, leak tests for the water bottle, food preservation tests for the container, and usability tests for the lunch bag).Iterate Based on Feedback:Gather feedback from personal use or trusted individuals, and make any necessary adjustments to improve the product's durability and functionality.6. Manufacturing SetupSelect a Manufacturer:Research and approach manufacturers who specialize in producing your product types. For each item:Water Bottle: Find a manufacturer experienced in metalwork or injection molding.Glass Container: Look for glass production facilities with experience in food-grade containers.Lunch Bag: Seek manufacturers who specialize in textiles or custom bags.Request Production Samples:Ask the manufacturer to create a small batch of products to ensure the production quality meets your standards.Review Costs and Feasibility:Negotiate production costs based on your target price point. Ensure the cost of producing a single unit is within your affordability range, considering materials, labor, and overhead.7. Prototype Evaluation and RefinementAssess Production Samples:Test the production samples for quality, durability, and usability again. Make sure there are no issues with the manufacturing process (e.g., flaws, weak spots, or material inconsistencies).Final Adjustments:If any issues are identified, communicate them to the manufacturer for corrections or adjustments.8. Production and Quality ControlOrder Initial Production Run:Once satisfied with the final samples, place an order for the first production batch.Quality Control (QC):Implement a quality control process to ensure consistency and durability in every unit. This could include inspecting random samples, checking measurements, and confirming material integrity.Packaging Design:Design simple and cost-effective packaging that protects the items during shipping. For example, reusable cloth bags, eco-friendly boxes, or minimal plastic packaging.9. Shipping and DeliveryLogistics Planning:Plan for the logistics of shipping from the manufacturer to your location. If you're dealing with international manufacturers, consider customs duties, shipping costs, and lead times.Storage:Determine how you'll store the finished products. Ensure they are kept in a dry, temperature-controlled environment if necessary (especially important for glass and fabric products).10. Ongoing ImprovementEvaluate Product Performance:After you've used the products for a period of time, assess their durability and functionality. Consider how they hold up to daily wear and tear, and think about any areas for improvement.Iterate on Design:Based on long-term usage, make any design improvements for future production batches. For example, if the water bottle dents too easily, consider a different metal or a thicker gauge.